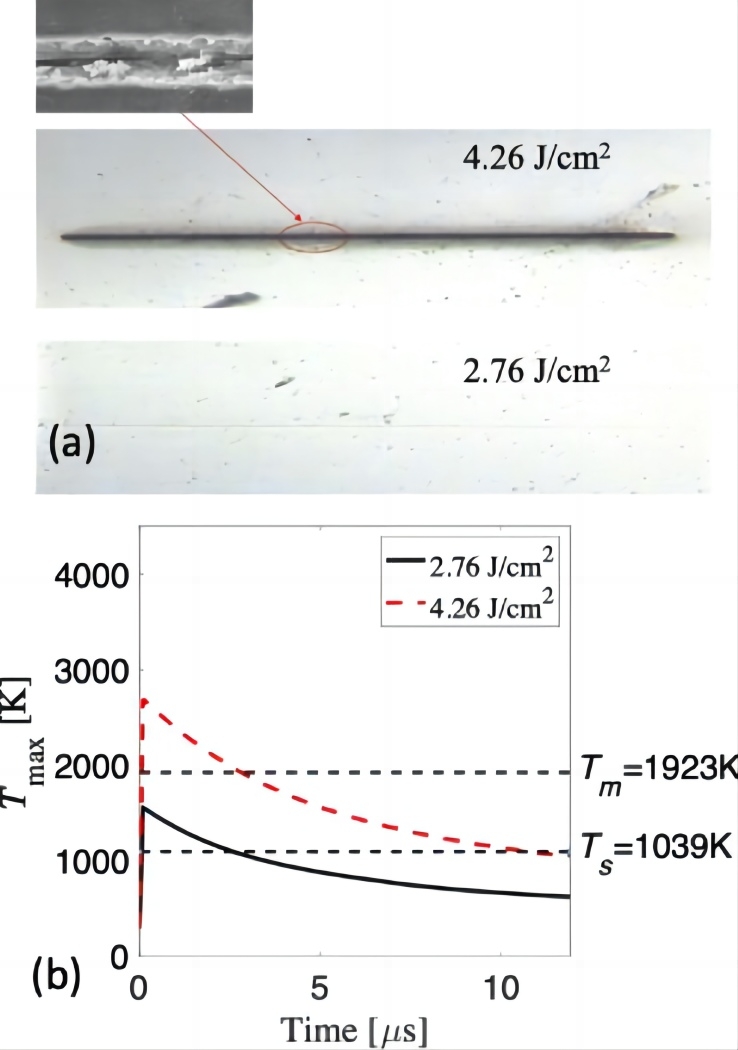
(a) Microscopic image of the processing based on line scanning, and (b) predicted surface temperature evolution for two laser fluxes.
In contrast, laser drilling technology has gradually become one of the mainstream methods for glass drilling due to its non-contact nature and high precision. Particularly, femtosecond laser drilling technology has shown significant advantages in this field. Femtosecond laser drilling utilizes lasers with extremely short pulse durations, which can generate high-intensity beams within the glass material without causing excessive thermal effects on the material's surface. This feature is crucial for reducing thermal stress and crack formation in glass, especially when processing thin or highly brittle glass materials.
In the automotive industry, glass drilling is used to create ventilation holes and decorative holes in automotive glass, while in the construction industry, it is widely used to produce decorative glass and safety glass. Traditional mechanical or ultrasonic drilling methods may pose risks of cracks and fractures in these applications, while femtosecond laser drilling effectively avoids these issues, improving the quality and safety of the finished products.
In the consumer electronics field, such as the glass screens of smartphones and tablets, precise glass drilling is also critical. The glass screens in these products require holes for cameras, sensors, and buttons, with extremely high demands on the position, size, and shape of the holes. Femtosecond laser drilling provides the high precision and quality required for these applications, ensuring both the aesthetics and functionality of the products.
In medical device and laboratory equipment manufacturing, precise glass drilling is equally important. The glass components in these devices often require the creation of precise fluid channels and connections, with extremely high requirements for hole accuracy and surface finish. Femtosecond laser drilling technology has demonstrated its unmatched precision and processing quality in these applications.
Another advantage of femtosecond laser drilling is its ability to precisely control the size, shape, and depth of the holes, making it especially important in applications that require high precision. This technology is particularly suitable for glass drilling that demands extremely high processing quality and complex shapes, such as in the manufacturing of microfluidic devices and precision optical components. In these fields, traditional drilling methods often fail to meet the required precision and quality, while femtosecond laser drilling technology can fulfill these high standards.
In summary, femtosecond laser drilling technology has demonstrated its unique advantages in the field of glass drilling. It not only surpasses traditional methods in terms of precision and efficiency but also opens up new application prospects in various industries. From automotive manufacturing to consumer electronics and medical device manufacturing, femtosecond laser drilling technology is gradually becoming an indispensable key technology in these fields.
References:
(1)Gong Chen et al. "Femtosecond-laser-enabled simultaneous figuring and finishing of glass with a subnanometer optical surface.." Optics letters, 47 15 (2022): 3860-3863 . https://doi.org/10.1364/ol.467413.(2)Jian-Guan Hua et al. "Laser-Induced Cavitation-Assisted True 3D Nano-Sculpturing of Hard Materials.." Small (2023): e2207968 . https://doi.org/10.1002/smll.202207968.
(3)Qing Luo et al. "Theoretical and experimental demonstration of transparent glass laser processing with a tripartite-interaction procedure." , 11437 (2020): 114370G - 114370G-8. https://doi.org/10.1117/12.2548304.
(4)Pierre Balage et al. "Crack-free high-aspect ratio holes in glasses by top–down percussion drilling with infrared femtosecond laser GHz-bursts." International Journal of Extreme Manufacturing, 5 (2022). https://doi.org/10.1088/2631-7990/acaa14.
(5)Shuang-shuang Li et al. "Femtosecond laser selective ablation of Cu/Ag double-layer metal films for fabricating high-performance mesh-type transparent conductive electrodes and heaters." Optics Communications, 483 (2021): 126661. https://doi.org/10.1016/j.optcom.2020.126661.