Glass cutting is a key technology used to precisely create cuts in glass materials, and it plays an important role in many fields. This technology requires not only maintaining the straightness of the cut but also minimizing material loss. Typically, glass cutting involves scoring a weak line on the glass surface and then applying pressure to cause the glass to break along that line. While traditional glass cutting methods, such as using diamond blades or carbide wheel cutters for scoring, are widely used, these methods can result in uneven cuts and unnecessary material loss. These limitations have led to the search for more advanced solutions.
In recent years, laser technology has been widely applied in the field of glass cutting. The principle of laser cutting glass is to use a high-energy laser beam to generate enough heat on the glass surface to soften or melt the glass, thereby creating a precise cut. Compared to traditional mechanical cutting methods, laser cutting offers higher precision and less material waste. In addition, laser cutting can provide smoother cut edges, reducing the need for subsequent processing.
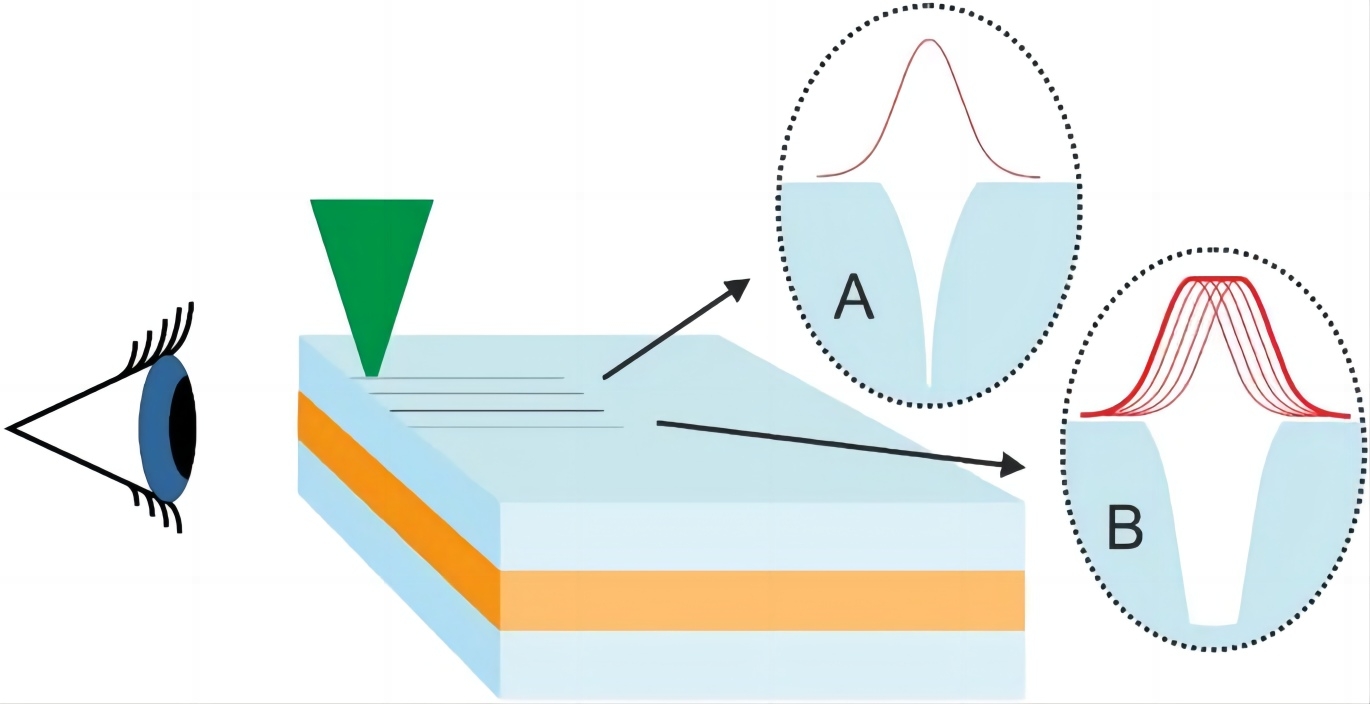
Schematic diagram of cutting test setups for a single cutting line
(A) and multiple cutting lines
(B). The cut is placed at the edge of the sample, allowing the results to be examined using an optical microscope on the left side wall.
Glass cutting technology has a wide range of applications in the construction, automotive, consumer electronics, and arts industries. In the construction industry, precise glass cutting technology is used to make windows, doors, and curtain walls, where strict requirements for the size and shape of the glass are essential. In the automotive industry, glass cutting is used to produce car windows and windshields, which must meet safety standards while also providing good visual effects. In consumer electronics, such as smartphones and tablets, precise glass cutting is used to make glass covers for touchscreens and displays. These products require extremely high standards of glass quality and precision to ensure a good user experience and device performance. Additionally, glass cutting is crucial in the creation of artwork, where artists use this technology to craft beautiful glass pieces, demonstrating the unique value of glass cutting in the arts.
In the field of glass cutting, femtosecond lasers are becoming increasingly important due to their high precision and control capabilities. Femtosecond lasers can precisely cut glass without inducing thermal stress, which is particularly important for reducing cracks and fractures. Because of the extremely short duration of femtosecond laser pulses, they can cut through the glass material without generating excessive heat effects on the surface. The advantage of this technology is its ability to achieve fine cuts, whether for straight lines or complex curves. Additionally, femtosecond laser cutting can reduce or eliminate subsequent processing steps, such as edging or polishing, thereby increasing production efficiency.
Femtosecond laser cutting technology is particularly suitable for cutting complex shapes or very thin glass materials, such as smartphone screens or other precision optical components. In these applications, the requirements for cutting precision are extremely high, and even the smallest error can affect the performance of the final product. The use of femtosecond lasers also offers more flexibility and design possibilities for glass cutting, allowing designers and engineers to explore new innovative designs.
In summary, glass cutting technology plays a critical role in modern industry and artistic creation. With the development of femtosecond laser technology, the precision and efficiency of glass cutting have been significantly improved, bringing new possibilities and enhancements to various industries. Femtosecond laser cutting technology not only improves the quality of glass processing but also provides unprecedented flexibility and innovation in design and manufacturing processes.
References:
(2)J. Sanabria et al. ">100-W 343-nm UV industrial femtosecond laser." , 11676 (2021). https://doi.org/10.1117/12.2579364.
(3)Jian-Guan Hua et al. "Laser-Induced Cavitation-Assisted True 3D Nano-Sculpturing of Hard Materials.." Small (2023): e2207968 . https://doi.org/10.1002/smll.202207968.
(4)Gong Chen et al. "Femtosecond-laser-enabled simultaneous figuring and finishing of glass with a subnanometer optical surface.." Optics letters, 47 15 (2022): 3860-3863 . https://doi.org/10.1364/ol.467413.