Milling of Complex 3D Structures is a highly precise machining technology that plays a crucial role in modern manufacturing. The core of this technology lies in the use of Computer Numerical Control (CNC) milling machines, which precisely control the movement of cutting tools along three-dimensional paths through advanced software control systems, enabling the cutting of complex shapes in bulk materials. This process requires not only that the machine itself has high precision and reliability, but also that the cutting tools and cutting parameters (such as speed, feed rate, and cutting depth) are precisely matched to ensure the quality and accuracy of the final product.
Multi-axis synchronized control is a key feature of complex 3D milling technology. In traditional three-axis milling machines, the workpiece or cutting tool can move along the X, Y, and Z axes. In multi-axis milling machines, additional rotational axes (such as the A-axis and B-axis) are added, allowing the workpiece or cutting tool to perform more complex rotational and tilting motions. This multidimensional movement capability greatly expands the possibilities of milling processes, enabling the machine to produce parts with complex curved surfaces and hard-to-reach internal structures, which is crucial for industries such as aerospace, automotive, and mold manufacturing.
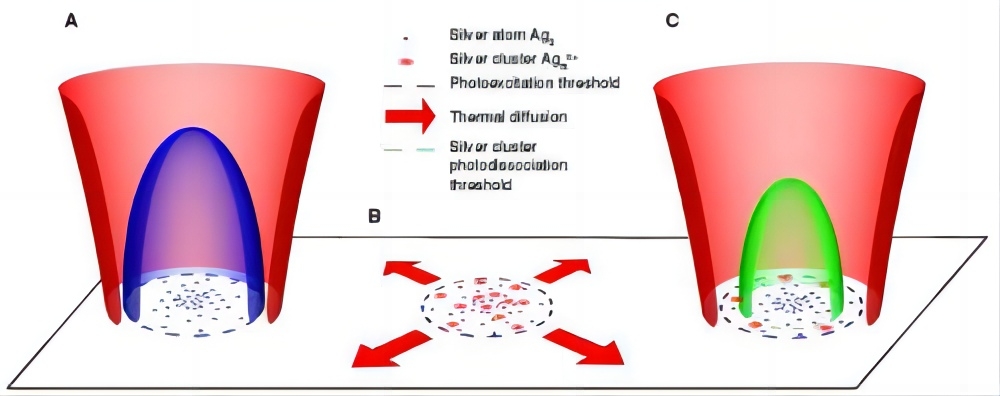
Figure 1. Schematic of nanostructure formation. (A) After laser irradiation, the released photoelectrons are captured by Ag ions, forming silver atoms Ag+0, represented by blue dots. The Ag0 distribution follows the interaction region defined by the blue dashed circular boundary. Due to the nature of nonlinear interactions, this area is smaller than the laser beam size. (B) After 1000 pulses, the local temperature rises and diffusion occurs, as indicated by the red arrow. The interaction between Ag0 and Ag generates silver clusters Ag+m x+, shown by the red dots. (C) Subsequent laser pulses photodissociate the newly formed Agm x+, leaving a cylindrical nanostructure composed of silver clusters at the edge of the interaction area. The photodissociation threshold of silver clusters is represented by the green dashed circle.
In the aerospace field, for example, milling of complex 3D structures is used to produce components with highly complex geometries, such as turbine blades and engine casings. These components require not only extremely high structural strength and fatigue resistance but also surface finish and dimensional precision that meet stringent standards. In the automotive industry, this technology is used to manufacture complex molds and parts, such as gears and transmission system components, which have very high requirements for precision and reliability.
The field of art and architectural design is also increasingly adopting complex 3D milling technology to create artworks and architectural models with unique designs and intricate structures. The flexibility and high precision of this technology allow designers to transform their creative ideas into tangible works, whether it’s a complex sculpture or a delicate architectural model, all made possible by precise milling technology.
With the continuous advancement of technology, femtosecond laser milling, as a complement and alternative to traditional mechanical milling, is beginning to show its unique advantages in specific application scenarios. Femtosecond laser milling uses extremely short laser pulses to achieve fine processing of materials, which is particularly important in the manufacturing of medical devices and micro-electromechanical systems (MEMS) that require extremely high precision and microscopic structures. Compared to traditional mechanical milling, femtosecond lasers can process materials without generating a heat-affected zone, a significant advancement for sensitive materials that are prone to deformation or damage due to thermal effects.
Additionally, another notable advantage of femtosecond laser milling technology is the wide range of materials it can process, from traditional metals and plastics to advanced ceramics, composite materials, and even biological tissues, all of which can be finely processed using femtosecond lasers. The versatility and high precision of this technology give it great potential for applications in modern manufacturing, particularly in high-tech industries that pursue exceptional performance and innovative design.
In conclusion, milling of complex 3D structures, whether through traditional mechanical milling or modern femtosecond laser milling, plays a crucial role in modern manufacturing. These technologies not only drive the development of manufacturing techniques but also provide vital support for the production of innovative designs and high-performance products. As technology continues to develop and application fields expand, the scope and influence of complex 3D milling technology will only continue to grow.
References:
(1)Y. Fuentes-Edfuf et al. "Ultrafast Electron Dynamics and Optical Interference Tomography of Laser Excited Steel." Laser & Photonics Reviews, 16 (2022). https://doi.org/10.1002/lpor.202200511.(2)F. Ceccarelli et al. "Low Power Reconfigurability and Reduced Crosstalk in Integrated Photonic Circuits Fabricated by Femtosecond Laser Micromachining." Laser & Photonics Reviews, 14 (2020). https://doi.org/10.1002/lpor.202000024.
(3)B. Tordoff et al. "The LaserFIB: new application opportunities combining a high-performance FIB-SEM with femtosecond laser processing in an integrated second chamber." Applied Microscopy, 50 (2020). https://doi.org/10.1186/s42649-020-00044-5.